ABOUT US
Made in Italy to ensure quality and cutting-edge technology
CIS is a family company with offices and plants in the southern Roman hinterland and is the main point of reference on the telecommunications market worldwide.
In 43 years, we have turned from a family business into an integrated company with highly specialised technicians, who are able to provide innovative solutions and excellent services for the telecommunications market. Our goal is to provide our customers with the best service and quality. With this aim in mind, the entire production process (from the idea to the final product), is completely carried out in our 10,000 square metre facilities, located near Rome.
Since the beginning of our activity, CIS has served more than 800 clients in four different continents, filed more than 200 patents and delivered countless innovative projects. Since 1980, CIS has been the official supplier for all Connectivity products for TIM and other telephone operators.
Sustainability and circular economy
The raw materials we use in the production of our products have all Italian or European origins, strictly CE certified and, therefore, always produced in compliance with labour and environmental protection regulations. During the production process, we use 30% of renewable energy, thanks to our advanced solar systems. All our machines are cutting-edge A+ class, for a minimal energy consumption and environmental impact. 100% of metal and plastic production waste is later reintroduced in the production process.
CERTIFICATES
Ensuring the quality of our work
Quality
With the aim of achieving full Customer Satisfaction, CIS operates in line with the perfect integration of the Quality System, adopting and effectively implementing a Quality and Environmental Management System within each phase of the Company process. This guarantees an excellent final quality of both Products (on the overall performance and lifespan) and Services, from those essential for the success of the production process, to those related to the provision of actual performances.
La piena consapevolezza e totale convinzione che il patrimonio più prezioso e di vitale importanza per un’Azienda sia costituito dal Cliente e dalla sua fidelizzazione, hanno da diverso tempo orientato le nostre scelte ed accresciuto il nostro impegno verso un’attività finalizzata alla piena “Customer Satisfaction” come, per altro, suggerito anche dalle Norme ISO 9001.
Risultati importanti in tal senso sono stati ottenuti attraverso un’azione mirata al coinvolgimento globale a tutti i livelli di tutte le componenti funzionali, interne ed esterne dell’Azienda, coinvolte nei processi.
La costante azione di sensibilizzazione dei Fornitori (percepiti come Partner nel processo produttivo aziendale), un’adeguata preparazione dei collaboratori interni di tutte le funzioni e di ogni livello, una spiccata attenzione ad ogni possibile contributo dei singoli, un proficuo interscambio delle informazioni funzionali all’erogazione delle prestazioni di ogni singola parte ed un adeguato coinvolgimento attivo del Cliente sono componenti indispensabili ed irrinunciabili per il raggiungimento degli obiettivi di crescita aziendale.
Al fine di garantire un costante miglioramento del livello di qualità del servizio erogato e, comunque, almeno in linea con le attese del Cliente, è stato appositamente predisposto un processo di monitoraggio in grado di misurare, pesare e valutare il livello di soddisfazione percepito all’esterno dell’Azienda relativamente ad ogni fase del processo.
Alte prestazioni di prodotti innovativi di elevate qualità ed affidabilità, possono essere ottenute e garantite solo attraverso il coinvolgimento attivo e responsabile di tutte le funzioni Aziendali che consenta:
• un’adeguata scelta delle materie prime già in fase di progettazione
• un’opportuna ottimizzazione dei processi produttivi pensati già in fase di sviluppo del prodotto
• constant training and updating of all internal and external collaborators (Suppliers)
• a ceaseless control and verification action to supervise all the processing stages, the tools and production equipment.
In questo ambito, la Direzione Aziendale promuove ed incoraggia un’incessante azione di miglioramento continuo.
Through the adoption and effective implementation of a Quality and Environmental Management System, CIS is fully committed to preserve and guarantee environmental protection, to prevent environmental crimes and to pursue the constant improvement of the IMS and its performance, by minimising the risks related to its performed activities, products and services.
CIS operates in the following fields:
• design and assembly of mechanical, electronic, thermoplastic and optical products and components for mailing and telecommunications services, assembly of railway signalling products with a UNI EN ISO 9001 standard certified management system
• design, production and assembly of mechanical and thermoplastic products and components, optical fiber cables for mailing and telecommunications services, production and assembly of railway signalling products with a UNI EN ISO 14001 standard certified management system.
We implement the following Company Policy goals every day and at every stage of our work:
• attuare in maniera sistematica i principi e le prescrizioni previste dai documenti del Sistema di Gestione Integrato (Qualità e Ambiente);
• operare assicurando efficacia, efficienza e affidabilità dei servizi forniti rispetto alle esigenze/requisiti espresse nei documenti contrattuali;
• understand the needs and expectations of our Customers and stakeholders and ensure their full
implementation;
• operare rispettando quei requisiti di tutela ambientale e di responsabilità sociale, che costituiscono una parte fondamentale del nostro vivere civile, con riferimento ai principi della prevenzione e del miglioramento continuo;
• rispettare leggi, norme e regolamenti, requisiti legali e altri requisiti vigenti, relativi ai settori in cui la Società svolge le proprie attività e soddisfare i propri obblighi di conformità relativamente alla Qualità, all’Ambiente;
• aumentare la propria professionalità, migliorando l’immagine verso l’esterno;
• operate towards a constant improvement of the IMS;
• determinare i rischi derivanti dalle proprie attività e il loro impatto significativo ed eliminare i rischi, in relazione alle conoscenze acquisite in base al progresso tecnico e, ove ciò non sia possibile, ridurli al minimo, possibilmente agendo sulle cause che li hanno generati;
• effettuare un monitoraggio dei processi, rischi/opportunità e degli aspetti/impatti ambientali;
• evitare sprechi e consumi non necessari di energia e di risorse naturali, inclusa l’acqua;
• use, whenever possible, environmental criteria when choosing packaging and consumables;
• contenere la generazione di rifiuti, con particolare riferimento a quelli pericolosi, partendo dalla fonte, in ogni lavorazione/processo e favorire una gestione dei rifiuti secondo una scala di priorità che privilegi, ove possibile il riutilizzo, il riciclo e il recupero;
• monitor and reduce CO2 emissions into the atmosphere;
• adopt the best techniques and procedures for emergency prevention and control;
• aumentare il livello di consapevolezza per perseguire un’efficace azione di prevenzione;
• comunicare in modo trasparente le proprie prestazioni ambientali alla comunità locale, alla clientele e a tutte le parti interessate per ottenere e consolidare la fiducia nei confronti delle attività e dei prodotti/servizi offerti;
• perseguire un atteggiamento aperto e costruttivo nei confronti del pubblico, delle Autorità Pubbliche e delle parti interessate;
• riesaminare periodicamente la Politica, gli Obiettivi, i Traguardi di Sistema e relativi programmi di attuazione e darne adeguata visibilità all’interno dell’azienda.
Tali obiettivi, oltre che essere costantemente monitorati nel corso dei lavori, vengono analizzati e riesaminati in sede di Riesame del Sistema di Gestione dalla Direzione con i Responsabili delle Funzioni e/o unità della Società.
Per gli obiettivi a breve termine, la Società ha predisposto apposito documento al fine di determinare specifici indicatori del Sistema di Gestione Qualità e Ambiente (pianificazione e monitoraggio obiettivi). I dati registrati su tali documenti vengono analizzati in sede di Riesame del Sistema di Gestione di volta in volta, se necessario, vengono fissati nuovi obiettivi/indicatori.
To achieve the company's objectives, the Management is committed to:
• assicurare che la Politica Aziendale sia sostenuta a tutti i livelli dell’organizzazione della Società e sia appropriata allo scopo, alle dimensioni e al contesto dell’organizzazione e alla natura specifica dei suoi rischi e opportunità;
• provide the necessary resources for the objectives’ achievement;
• incoraggiare il miglioramento continuo delle capacità individuali di ogni collaboratore – dipendente (miglioramento clima aziendale);
• periodically review the Company Policy in order to ensure its constant adequacy.
I requisiti e le modalità di attuazione del Sistema Gestione Integrato (Qualità e Ambiente), contenuti nella documentazione del SGI medesimo, delineano la Politica Aziendale della Società, di cui ne viene pertanto richiesta la completa osservanza da parte del personale nell’ambito delle rispettive competenze e responsabilità, tenendo sempre presente che la Qualità delle attività svolte è compito specifico di chi esegue e non di chi controlla.
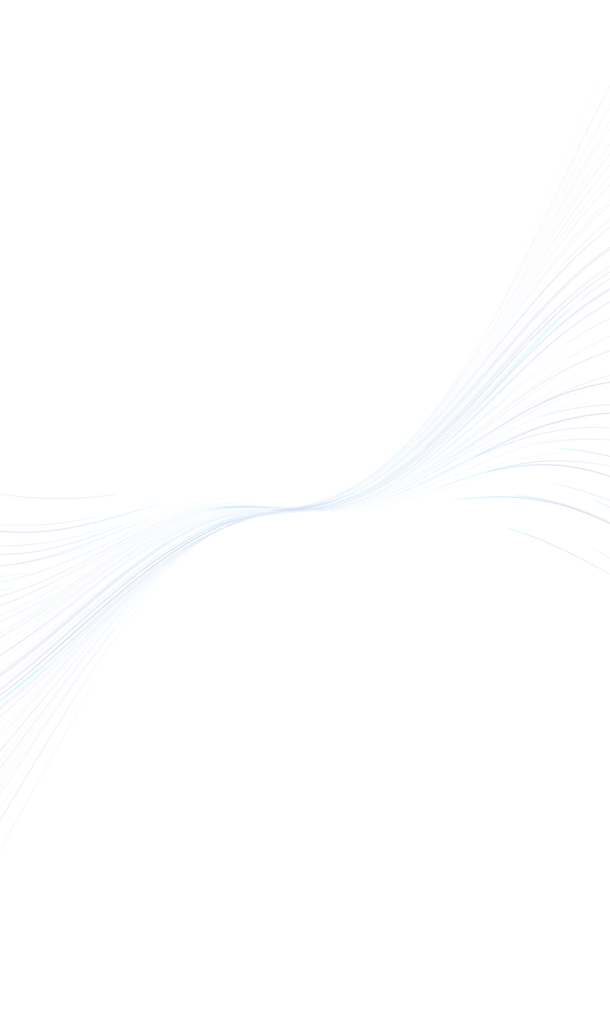
If you are interested in our products and services, we will be happy to hear from you
CONTACT US